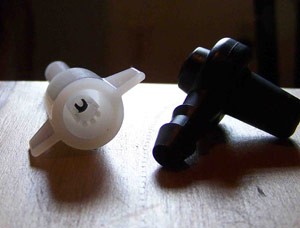
it slides into. Note white color is for demonstration
purposes. Working model will be black.
Each year the Vermont Maple Sugarmakers’ Association holds its annual Maplerama event – an excuse for sugarmakers from around the state to get together, talk shop, and get excited about the upcoming season. The buzz at this year’s banquet was the new check-valve spout, developed by Dr. Tim Perkins at UVM’s Proctor Maple Research Center. During a field test last spring, the spouts produced a seasonal total of 44.6 gallons of sap per tap on 23.5 inches of vacuum. This sap boiled down to make 1.09 gallons of syrup per tap. Conventional wisdom holds that an efficient producer should make between 1 quart and ½ gallon of syrup per tap on a good year (producers with gravity systems and/or immature sugarbushes may have averages considerably lower than that). As you can see from the numbers, we’re talking about a 50- to 70-percent increase in production – a warm and giddy notion that has a sort of Big Rock Candy Mountain feel to it.
The science behind the new spout is brilliantly simple. As the name suggests, the spout contains a check valve – a tiny plastic ball that rolls forward and backward within the unit. When the sap’s flowing, the ball seats between plastic fingers on the backside of the spout, thus allowing sap to flow around it and into a tubing system. When the sap’s running backwards, however, the ball valve shoots forward and seals the operating end of the spout, thus keeping sap from backwashing into the tree. This prevents microbial contamination in the taphole; a cleaner taphole extends the sap-flow period, thus the big production numbers.
If you’re not familiar with vacuumized tubing systems, you’ll wonder why sap would run backwards through a sap line. What happens is negative pressure develops inside the tree after an extended period of running a vacuum pump. At the end of the day, if you shut off the pump before freeze-up, any liquid that’s in your lines will be drawn backwards toward the negative pressure in the tree. This can happen on a smaller scale if a leak develops in a line, or each time your releaser dumps.
And so this new spout has the potential to revolutionize the industry. Some caveats:
It should be noted that sugarmakers without vacuum systems won’t see any increased production from these spouts. Gravity systems shouldn’t backwash like vacuum systems do.
It should be noted that the spout was only field tested for one year.
It should be noted that the Proctor bush, where the spout was tested, is a Cadillac operation. There were new droplines on each spout; lateral lines averaged between one and three taps per line. In short, no one with an antiquated tubing system should expect that the spout alone will result in gallon-per-tap yields.
It should be noted that the scientist, in this case, is also the salesman.
And just because it’s a drizzly morning, I’ll also wonder aloud whether – if this spout proves to be as good as advertised – our maple markets are healthy enough to support such a dramatic increase in production. 2007 was a great year for sugarmakers who had syrup to sell. A shortage of syrup in Canada pushed bulk prices through the roof. As per the basic rules of business, production increased dramatically last year, and bulk prices came down considerably. I’m no economist, but it seems that in the short term, anyway, a new technology with the potential to increase yields substantially needs to be considered in the context of a world-wide recession, where demand may not be in line with supply. Aren’t there examples in the dairy industry where increase-your-yield technology turned out to be a double-edged sword?
Of course, any business-minded person would scoff at such pessimism. They’d call it unimaginative; a fair charge. And none of this should overshadow the main point: that Tim Perkins and company have developed an exciting new product. We just ordered a pile of these new spout adaptors and will soon get to work upgrading our main sugarbush. If you’re a fellow sugarmaker, let’s compare notes next spring.