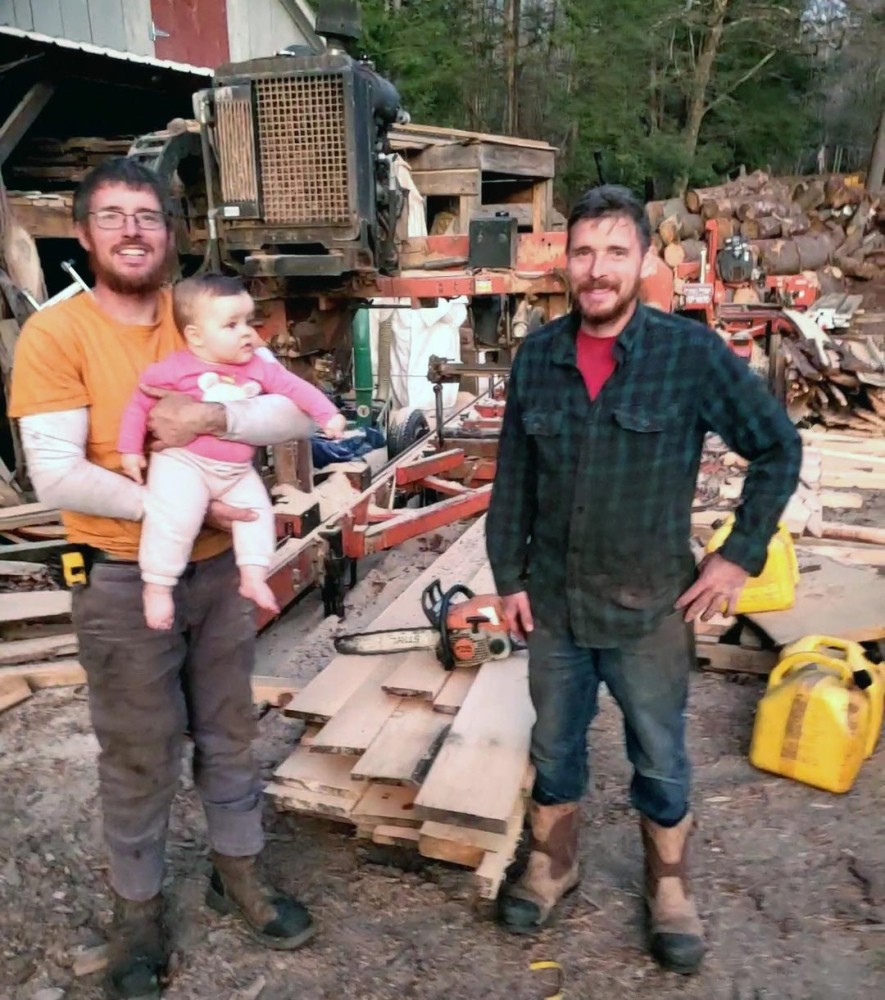
As kids, Jay and James Clarke traveled to state fairs and jobsites with their father and his portable sawmill. The twin brothers bought their first mill together as teenagers and settled into work as the J Team. The business now includes three mills, and its services range from on-site milling on clients’ land to re-siding old barns and sawing wood for a timber framing school.
What are some of your memories of spending time outside while you were growing up?
Jay: We grew up in Ashfield, Massachusetts, in an old farmhouse with 100-something acres. We’d run around in the woods, just having fun. We would take down the dead pine trees and build teepees and stuff like that. We often went with our dad to jobsites. We would do our homework in a little tree fort platform at one job.
James: Our dad had a sawmill when we were growing up, and he’d take us all over the place, so we also grew up in all sorts of fairgrounds and jobsites and whatnot. At the fairs, our dad would demonstrate the sawmill to show how it operates. We still do that for a few fairs and we mill a lot of wood for the fairgrounds, too. So, we’re helping the fairgrounds fix stuff up, and that means a lot to us, because we grew up around them.
When – and why – did you decide to buy a sawmill?
James: We decided to get our sawmill at age 17. Our grandmother had left us some inheritance, and with that and what we’d saved from our farm work over the summers, we had enough to buy a sawmill. We were working on a fort, and we needed wood for that, so we decided to buy a sawmill. There was enough push from enough people in our lives that it made sense.
Jay: We always thought it would be fun to have a mill. For the first few years, we just sawed in the yard. We’d do a lot of grade stakes or whatever local farmers needed for lumber. That’s what kept us busy.
What was the learning curve like for running that first mill?
James: Our dad never taught us to run the mill. We were completely self-taught, but it was safe enough for two 17-year-olds to figure out. I also lived in Tennessee for a year and ran a mill down there. I had a mentor who moved to Tennessee, and I followed him down there to learn homebuilding. But it took all sorts of turns. I ended up talking to a big sawmill down there and milling a ton of wood for them. Then I brought all that experience back to Mass with me.
Jay: Wood-Mizer gives you a 1-hour demo when you purchase a mill. It’s a very safe mill. It’s not like a circular mill, where you’ve got the big blade spinning out in the open. It’s basically a bandsaw on a track, and you’re standing behind it. So everything that goes wrong is on the other side of a bunch of steel. As long as you’re smart around the logs – that’s the hardest part. I don’t do any tree work. I prefer them on the ground – that’s enough excitement for me.
Where did the name come from? And what are some of the things the J Team does?
Jay: We were working for a farmer packing corn, and they couldn’t tell us apart, so they just called us the J Team, because we would work hard. That’s actually where we made money to purchase the mill. We just stuck with that name, because we didn’t know what to call the business. We each handle a different side of the business, although it’s flip-flopped over the years. I do the portable side of it, so I’ll go to people’s places and mill for them. Jamie does more of the lumberyard side at this point.
James: So much of our work has grown from word of mouth and customers we’ve built up over time. There’s a timber framing school, the Heartwood School in New Hampshire, and we’ve started milling some frames for them. I didn’t go looking for them. They came to us, and it’s been a huge amount of work. I also re-side barns for farmers. That started because there was a guy who wanted us to mill a bunch of reclaimed barn beams, because he was tearing down barns. And he asked if we could supply the siding for him to re-side barns. That’s another thing we just sort of fell into. It’s been a lot of dumb luck.
How has the business changed over the years?
Jay: We have three mills now and three guys to run them – the two of us and another guy, Adam. I run our oldest one. I’m a mechanic, too, so I’ve been keeping it running. It’s modified, so it’ll cut 62 inches wide. I do all the weird stuff. My brother has the best mill Wood-Mizer makes. That’s the production one here. I’m making do with my mill for now, but we’ll be upgrading next year. So then we’ll have four mills and three guys to run them.
James: It’s nice having a spare mill. Jay’s mill is portable only. My mill doesn’t move anymore. And the other mill does a mix of both, depending on what’s needed. Right now we’re milling like crazy here. For the timber framing, I have to source the logs on my own. Whatever they need, if I don’t have quite enough, I’m running around trying to find it. For years, we just got whatever wood tree services would bring us, and some would give us the whole mix of whatever they had – from junk all the way up to beautiful stuff. Then I started buying from one tree service who was reliable and would have what I need. Then I finally got over my fear of talking with loggers. I always figured loggers deal with massive sawmills and wouldn’t want to deal with me. But there’s a logger named Nathan Clark, and I’ve been working with him a lot, and he’s fantastic. I respect his time, and he respects me, and it works well.
What are some of the challenges of running a sawmill – or three sawmills?
Jay: I think a lot of the challenges we have are related to logistics. For me, it’s moving the log to the mill, then moving the lumber off the mill. I’m always pushing the limits of what the mill can do. I’ll show up with just the mill and some farm jacks and make 50- or 60-inch cuts in logs for slabs. I’ve had jobs with a 9,000-pound log that I get on the mill with hand tools. And also just getting the mill set up and in place. I finally have a tractor that I take to jobs. I drive a Nissan Frontier. The tractor’s not too big, it weighs about 4,000 pounds, and the mill doesn’t even weigh 4,000. My brother and Adam both have F-250s if I need a bigger truck.
James: On my side, there are so many different types of wood and so many different uses. Some wood works well for this, some works well for that. You can’t use red oak for outdoor stuff, but you can use white oak because it’s rot resistant. Black locust is a common wood around here, and it’s the most rot-resistant wood we can find, but you’ll get ant holes right up through the center of the tree, and you won’t notice until you get almost down to the beam you need. Jay gets to go to a jobsite and mill whatever they have to whatever they want, and it will all work out, whereas I have to care about what every single type of wood I have in the yard, and all the little details of how that works. For instance, Heartwood doesn’t want sugar maple for bracing in the frame, because it moves so much more than every other hardwood we have. There’s a lot of intricacy to balance. There are a lot of different kinds of trees, and they don’t come with labels attached to them like at Home Depot.
What are some of the perks of the work you do?
Jay: For me, I think it’s making use of my engineering training, but also working with wood, which is back to our roots. I’ll show up to a job with my little truck and a little mill, and sometimes I can tell people think I’m there just to saw the little stuff. Impressing people is a lot of fun. And I’ll travel all over. I’ve been way out onto Cape Cod and out by Lake George, so I get to see the sites, too – it’s not just working locally and milling local trees. I meet a lot of characters.
James: I appreciate being able to mill all kinds of wood and seeing all kinds of beautiful grain, and figuring out how to cut it to get the nicest look. I save a ton of stuff for woodworking, and having an infinite supply of really fun stuff is a bonus. I’ve been woodworking for 13 or 14 years now, mostly small stuff that doesn’t take a lot of precision or measuring – spatulas and spoons and bowls. We sell a lot of stuff at the fairs that we bring the sawmill to. The best part of the job is the people we get to meet. It’s also nice that we still deal with customers our dad worked with. He passed away when we were 19. There’s a lot of people who care about us and our dad and just seeing that we’re still carrying this on.