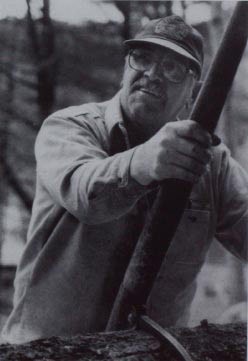
Years ago a fellow traveled around central Vermont with a circular saw mill and charged for his work by counting the number of times he poured five gallons of gas into the tank of his sawmill engine. Another travelling sawyer who worked in the Connecticut River Valley in the 1970s had his mill mounted on the frame of an old bus.
The concept of a traveling sawmill is not new. In the old days a conventional sawmill would often be set up on the landing of a big logging job for several months before moving on to the next job.
But the pre-1980 portable sawmill was typically a bulky affair, more like a take apart stationary mill than the self-contained, lightweight models of today. Nearly all of the portable sawmills now being manufactured are bandsaw mills, with blades that are relatively easy to maintain and inexpensive to replace when old age or an overgrown sap spout strikes.
Wood-Mizer, by far the biggest manufacturer, produced its first mill in 1982. Now they turn them out at a rate of 40 a week and have sold over 11,000 sawmills. Wood-Mizer mills are in use in 80 countries and they have a factory in Poland. In Vermont, Wood-Mizer salesmen have been quite successful and Bob deGeus, who monitors sawmills for the Division of Forestry, estimates that there are well over 100 here, of which all but about 30 are "very part time.”
Don Lawrence, a portable mill owner from Sharon, bought one of the first Wood-Mizers. A tinkerer very much in the Vermont tradition, Lawrence devised several improvements to Wood-Mizer mills. When the price of kerosene rose, Lawrence tried water instead to lubricate his saw blade. Now a water dripper is standard Wood-Mizer equipment. He also got tired of having to change drive belts to adjust the forward motion of the saw and used an old truck handbrake lever as part of a gadget which changed the speed more simply. Wood-Mizer used that idea (but not the handbrake) as well.
At least two other brands are used in the state. The first of the new generation of portable mills was made by Warren Ross and is a simple machine. Ed Huling, of Sheffield, bought one about seven years ago and his family has used it for a number of building projeas. Now his wife has taken over as the family sawyer. Production is far slower on the Ross Bandmill, but at less than $5,000 it doesn't take as long to pay for itself as does a Wood-Mizer, which is priced from about $7,000 to $17,000. The Ross Bandmill is not something you would use to make aliving, but it is a nice addition to the tree farm.
At the other end of the scale, the rugged Min-Max, made by Sanborn Machine in Maine, is more than twice as expensive as the Wood-Mizer and is more often used as a stationary production machine in small commercial operations than as a moveable mill.
Some sawyers do the logging as well. Paul Ruta, from Plainfield, has a two-horse power team and a 18-horsepower portable mill. Both the logging and sawing take place slowly and might be a good choice for a small job. Being able to do both has enabled him to find work when others who only log or only saw were having to scramble.
Ruta clearly likes the slower pace, saying it "allows the logger, landowner and forester to check on the job and re-evaluate the work."
Small bandsaw mills often visit small furniture makers, who can specify exactly how they want a log sawn to suit a particular project.
Another niche that can be profitably filled by a portable mill is sawing wood at the top of the line. Dan Ludwig, from Fairlee, saws a lot of high quality hardwoods.
Working alone gives him the chance to examine each log and think twice about each cut if he needs to. "At a regular mill, the sawyer can't stop and think," said Ludwig. "Five guys are standing around doing nothing while he scratches his head."
These portable mills quickly filled the gap left when small farm sawmills went the way of many of our small farms.
Your own boards
Some of the benefits of getting an accurate, inexpensive sawmill right in your backyard have great appeal. The energy and environmentally conscious among us can get some satisfaction by buying locally grown lumber which is contributing to the local economy. By milling your logs on your land for your building projects you may even kindle visions of yourself as a 20th century Thoreau.
On a more practical level, there are no trucking costs. Just trucking logs to a sawmill typically costs about four or five cents a board foot and uses fossil fuels. Most portable sawmill operators don't charge very much to move their equipment to your site and setting up usually takes only 15 or 20 minutes. Most will saw as little as 1,000 board feet without complaining.
You can get more lumber from your logs. Bandsaws like the Wood-Mizer are in fact miserly. At each pass of the blade these saws convert only 1/16 to 1/8 inch of log into sawdust, compared to the 3/8 inch kerf of a circular saw blade. This difference is much greater if you are cutting 1x4 boards than when you are only making the few cuts required to turn out an8x8 beam. Overall, you can expect to get from 12% to 15% more board feet from a log when using a bandsaw mill instead of a circular sawmill.
Because of the smaller kerf, bandsaw mills require less power. Also on the plus side, these mills are quite accurate, leave a smooth surface and are generally acknowledged to be quite safe.
Acceptable boards can be made from poplar, red pine, hemlock, and from standing dead trees which are still sound. Mills often are not interested in these products at all or pay low prices for them, but a portable mill may be able to turn out just what you need.
You can totally ruin everything you have sawn by improper drying. Hardwoods are more prone to develop defects than softwoods, partly because the total shrinkage is generally greater. Some warp is inevitable and you may want to saw hardwoods oversize to be sure you can get the final planed thickness that you want.
Freshly sawn lumber must be quickly and carefully stickered, using dry stickers every 16 to 18 inches or, according to some, as close as every 12 inches for hardwood lumber. The purpose is mainly to separate wet boards and to allow air circulation, but the wood's own weight in the pile helps control warping. Using stickers at the ends of the piles reduces end checking as well as warping. Large numbers of carpenter ants will sing your praises if you neglect to put a roof on your lumber pile.
On the job training
With help from portable sawmills, landowners Ben Bradley and Tii McLane produced much of the lumber for five houses built at Blue Moon, a land cooperative in Strafford. All of the house sites were wooded, and much of the wood was low grade pine which was in the way and would have been difficult to market. The clearing imperative initiated the idea of on- site milling, but they went on to thin an adjacent pine stand and use that lumber as well.
They also milled out 4 inch x 5 inch hardwood beams to use in their first floor ceilings. McLane used sugar maple, yellow birch, ash and paper birch for her beams and says they are the most satisfying part of her house. "I could never have considered buying them from a mill and I enjoy knowing exactly where they came from and what they looked like as trees,' she says.
They do, however, remember several lessons that they learned the hard way. One is that you must have the tree species and quality that you need for your project. Their pine was of low quality and they discovered that 2 x 4s made from crooked pines never do figure out what straight means. Their 2 x 6s were better, but not great. Larger timbers, made from the center of the log, came out very well. They are stressed evenly on all sides and the impulses to warp cancel each other. Spruce would have been much more suitable, but, unfortunately, the nearest spruce to their job would have involved a timber trespass.
Some products that are hard to sell as logs are hard to sell for a reason. In addition to being time consuming at building time, there is more waste generated when you use log that are bumpy, crooky or partly rotten.
You have to be organized from the start. Your cut list – the dimensions of all the lumber you want – much be ready before logging begins. Decisions about the final products are made as soon as a tree is felled.
McLane and Bradley have unpleasant memories of moving piles of logs because they were not decked properly and the sawyer could not get them onto his mill. Bradley's advice is that you should "get your sawyer to the site to tell you exactly how and where the logs should be piled."
Keep in mind that, however hard you try, there may not be a perfect match between your logs and your cut list. There will be leftovers and there may be defective boards, all of which you pay for.
Larger sized timbers tend to cost more per board foot at the lumberyard. Both landowner and portable mill sawyer can do better when sawing out larger timbers.
Even if you don't do your own logging, sorting and stickering boards takes time. You will be called upon to make decisions — and to clean up. Is getting rid of slabs and sawdust a chore, or are you delighted to have them in your sugarhouse or on your blueberry bushes, respectively? Remember that the money you could have gotten for stumpage should be in the arithmetic, if the arithmetic matters to you.
After using oxen, horses, a tractor, and a large skidder to supply a portable mill, McLane and Bradley advise that, regardless of what kind of equipment you use, you should do a small job first to get to know the situation. In spite of all their warnings, they would use a portable mill again, but they both laughed as they remembered that when the one professional contractor in their land cooperative built his house, he made a beeline for the store, not the portable mill.
For clean well-decked logs, saw operators will charge roughly from 14 to 18 cents/board foot for sawing. This compares to, again very roughly, about 30 to 35 cents for unplaned lumber in small sizes at your neighborhood sawmill. Larger sizes at the sawmill typically are 40 cents/board foot and up, but until you get into outrageous sizes, the per board foot price for at-home sawing stays the same.
A portable mill could be just the ticket if you need to clear your house site anyway, could not get paid stumpage for your trees, are looking for specialty products, or place little or no value on your time. If you are sawing larger timbers from unmerchantable logs, you've got it made. And remember, there are plenty of people who are perfectly content with the intangible benefits that a portable sawmill can provide.
Discussion *