Most days, Jesup Memorial Library Director Matt DeLaney toils in a tiny Harry Potter-esque office tucked beneath the stairs leading to the 114-year-old building’s second-floor balcony. The space is too tight for meetings, and it’s not clear whether the standing desk reflects his personal preference or is just a practical accommodation.
But on this particular day in late October 2024, as Bar Harbor, Maine’s fall foliage tourist season draws to a close, DeLaney dons a hard hat and stands outside the building as a small fleet of flatbed trucks negotiates the final street corner before entering the library’s parking lot. In a few minutes, workers will begin offloading cross-laminated timber (CLT) panels of eastern hemlock for a $9.1 million, three-story, 12,000-square-foot addition that will double the library’s original size.
The addition will house a large and welcoming entry vestibule, a 120-seat auditorium, a maker space, conference rooms, an office for the library’s Youth Services department, and a climate-controlled space for archives. What’s more, electronically activated doors and entryways and a new elevator will make both the addition and the original building more accessible to visitors with physical disabilities.
“This is a building that didn’t even have electrical outlets when it opened,” DeLaney said of the original Colonial Revival structure.
While he’s enthusiastic about the project’s sheer size, technology, and design for serendipitous interactions, it’s the innovative building material that inclines DeLaney to speak well beyond his “library voice” as he launches into the addition’s origin story.
“There was interest in mass timber and CLT since the very beginning,” he said. “But it was like nobody really knew what that meant. Our architect hadn’t built a CLT building. Our general contractor had never built with CLT. And while our structural engineers had designed a number of mass timber buildings, it has still been new for a lot of players on our team.”
The library addition is notable for another reason: it will be just the third building constructed using CLT from eastern hemlock, a species native to New England.
DeLaney got involved with the project about three years ago and has advocated for mass timber because it stores carbon for the lifetime of the building, and its production generates lower greenhouse gas emissions than other available building materials. He hopes that the library can serve as a model for environmentally sound construction practices and locally sourced, sustainable materials.
“We are in Bar Harbor. We have 4 million people coming to this island every year from around the Northeast, from around the state, from around the world,” he said. “If you want to tell the sustainable story of mass timber and CLT, and particularly eastern hemlock, this would be a great place to showcase it.”
A Short History of CLT
Mass timber as a construction material is not new. An article from the Forest History Society dates the first architectural use of glulam in the United States to 1934, when architect and engineer Max Hanisch, an immigrant from Germany, incorporated glulam arches into his design for a gym in Peshtigo, Wisconsin. According to Peggi Clouston, a professor in the Department of Environmental Conservation at University of Massachusetts Amherst, glulam usage appeared in local building codes as early as the 1940s. “But cross-laminated timber, which is the buzzword these days, only came out of Europe – Germany, Switzerland, Austria – about 30 years ago,” she said.
CLT became popular in Europe in the 1990s, and builders in Canada and the Pacific Northwest were quick to incorporate it into their structures. The first CLT plant in the United States, SmartLAM, opened in Montana in 2012. Since then, about two dozen facilities have sprouted across Canada and in the western and southern United States. What makes Clouston and others enthusiastic about CLT is that it can replace steel and concrete for building elements that aren’t a good fit for glulam. Like glulam panels, prefabricated CLT panels can be assembled quickly, reducing both time and waste on the job site. Unlike glulam, CLT has strength in two directions, making it better suited as a material for flooring, walls, and ceilings.
Clouston, who studied timber engineering at University of British Columbia, has experience working with mass timber as an engineer on stadium-scale buildings on the West Coast. She has encouraged her students and the northeastern building community to consider the virtues of CLT as a partial substitute for concrete and steel, citing both the wood product’s structural advantages and its environmental appeal. She said that she was surprised by the difficulty of making her case.
“I guess I was somewhat naive, because I hadn’t realized how hard it is to convince people with just photographs,” she said. “I was just pointing at these [photos] and saying that we could do this here.” When UMass Amherst began making plans for a new building to provide faculty offices, including offices for building and construction faculty, Clouston and others saw an opportunity to establish a prominently placed mass timber project that would showcase how to use heavy sections of wood in large-scale construction. They worked with U.S. Representative John W. Olver to obtain state and federal funds to develop a mass timber demonstration building. (A detailed description of this effort and photos of the construction project in progress are available in the Spring 2020 issue of Northern Woodlands.)
Completed in 2017, the Olver Design Building cost $36 million to build. It remains the most advanced mass timber structure in New England, with an exposed glulam frame, composite CLT-concrete floors, and CLT shaft walls. According to the university website, the building stores more than 2,000 tons of carbon dioxide. Since its opening, it has hosted dozens of regional conferences and gatherings of architects and engineers, who can see firsthand how mass timber offers an environmentally friendly structural material that is also beautiful to behold.
The Olver Design Building fulfilled Clouston’s ambition to inspire the local design community to consider mass timber as an alternative to concrete and steel. However, to fully realize mass timber’s environmental benefits, Clouston said, the Northeast’s building community will need to put greater emphasis on using regionally harvested wood.
Mass timber is a broad term for large-scale engineered wood-based products that can serve as structural material, and often, as a substitute for concrete slabs or steel beams.
Cross-Laminated Timber (CLT) is a form of engineered wood product comprised of layers of kiln-dried lumber, stacked in alternating orientations, and glued together with a structural adhesive. As compared to earlier forms of mass timber such as nail-laminated decking, CLT has greater dimensional stability, meaning it’s less apt to swell or shrink under moisture fluctuations. It’s also strong (can bear loads) in two directions and therefore appropriate for structural use in floors, roofs, and walls in mid-to-large sized building projects.
Glued Laminated Timber (glulam) is an earlier form of mass timber. The key difference between glulam and CLT is that in glulam, all the lumber layers are stacked and glued together in the same orientation. This manufacturing approach makes glulam beams appropriate for structural elements such as a columns, beams, and trusses, where the engineering need is strength in one direction.
Regional Sourcing
In theory, many species of trees, especially softwoods, could serve as CLT feedstock. But in practice, manufacturers want to use nearby raw materials. Given the trajectory of CLT in North America, it’s no surprise that western Douglas fir, Canadian spruce, and southern yellow pine were among the first to be certified to the American National Standards Institute/American Plywood Association (ANSI/APA) PRG-320 standard for structural CLT.
Mass timber advocates such as Clouston, industry leaders, and state and regional officials began to wonder if they might be able to reverse-engineer the economics, to kick-start a virtuous circle of resource management. What if you could certify some abundant local species for use in structural CLT panels? Would the allure of abundant raw materials, along with the end-user demand that the Olver Design Building and other projects had begun to generate, incentivize investments in a new CLT manufacturing facility in the Northeast?
Eastern hemlock, the fourth most abundant saw timber in Massachusetts, was particularly interesting to state officials looking for new uses for a low-value and underutilized species. One disadvantage of hemlock as a building material is its tendency to suffer from ring shake, a wood defect in which wood fibers separate between, and parallel to, growth rings. Ring shake not only makes lumber prone to breakage, but also makes it harder to process at the sawmill.
This defect was irrelevant to CLT, however, because fibers are already separated and reassembled as part of the manufacturing process. Eastern hemlock is a logical choice for CLT because it presents the opportunity to transform a low-value wood into a high-value material.
Underwritten by a state grant, Clouston and two colleagues published a research paper in the March 2020 issue of Journal of Materials in Civil Engineering that showed both eastern hemlock and eastern white pine could meet the ANSI/APA standard for CLT. In this and subsequent work, Clouston’s team confirmed that ring shake weakness in traditional lumber did not result in lower strength in CLT.
“Rather than make it experimental for manufacturers, we took the guesswork out of it by doing it in the laboratory,” Clouston said. “The papers that we wrote said to any manufacturer, ‘You’re not wasting your time here. You just need to get the lumber and fabricate it.’”
If the academic research had an immediate impact, however, it was not on faraway manufacturers but within the tight-knit New England forestry community, where advocates have long held the view that a well-managed, diversified, and productive forest is not just an economic asset, but essential to the region’s environmental and social well-being as well.
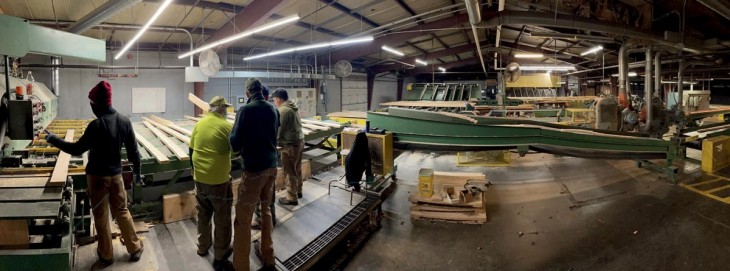
Cut to the Chase
“What we’re trying to do with this project is, obviously, get a manufacturing plant built in the Northeast that will use these northeastern species,” said Charles Levesque, president of Innovative Natural Resource Solutions, LLC, and the executive director of the North East State Foresters Association (NEFA). “Had [Clouston] not done her work, probably we would not have moved this project forward.”
The project – “Sourcing Eastern Hemlock CLT for Northeastern Mass Timber Building Construction” – provided the critical next step in bringing eastern hemlock CLT panels to the Bar Harbor library.
Funded in part with a $250,000 grant from the U.S. Forest Service’s Wood Innovations Program and additional support from the Commonwealth of Massachusetts and University of New Hampshire, the NEFA-led project harvested, dried, planed, and packaged some 34,000 board feet of eastern hemlock by the end of 2021. The logistics were complicated. Cersosimo Lumber, with headquarters in Brattleboro, Vermont, agreed to supply hemlock lumber to the project along with kiln drying, planing, and grading services but couldn’t fulfill the full amount needed. Parker Lumber in Bradford, Maine, and White Mountain Lumber in Berlin, New Hampshire, also contributed green wood.
Barry Kelley of White Mountain Lumber said the need to collaborate underscored eastern hemlock’s underutilization and scarcity within regional supply chains. Unless a species has a sufficient commercial market, loggers will leave it in the woods.
Once Cersosimo processed and graded the hemlock, it shipped the wood to SmartLAM’s CLT plant in Dothan, Alabama. There, over the next month, the plant processed it into “billets” – testing-size CLT panels – which it then sent on to the American Plywood Association’s testing facilities in Tacoma, Washington.
Levesque described an arduous review process. “They have almost 20 different tests that they do,” he said. “They’re measuring different strengths, bending and breaking in different directions, and from that they are able to determine the strength characteristics of the sample.” Confirming what Clouston’s team had previously documented, the APA tests showed that the drawbacks that make eastern hemlock less valuable as lumber have no impact on its use as feedstock for CLT.
To forestry managers, as with Clouston, eastern hemlock’s status as low-value wood made the project even more compelling.
“These are two complementary products,” said Andrew Fast, a forest industry specialist with University of New Hampshire Cooperative Extension. “Spruce-Pine-Fir South is a ready-made product for CLT. We have mills that can supply that, and it can go to the CLT manufacturer where someone can order it. Eastern hemlock is sort of the long shot where it’s a new supply chain…that we can build out.”
Fast, who worked closely with Levesque on the certification and demonstration project, said new products such as CLT can promote diversity in both forests and local economies that once were dominated by monocultural management.
“I just think the more versatile markets there are, the more resilient some of our sawmills are in terms of being able to send different material to different places, will give everyone more options,” he said. “And when you have more markets like this, it creates resilience in terms of the overall industry.”
From Testing to Building
By June 2022, the APA testing in Tacoma was complete. The report concluded that eastern hemlock CLT panels met the standards and were good to go. But go where?
If Phase 1 of the NEFA project was to prove Clouston’s research was on the mark and that eastern hemlock (and in the future, other regionally abundant species) could be used in structural CLT panels, Phase 2 was even bolder: use of hemlock CLT in new buildings.
Having scratched a planned design-build competition due to budget constraints, Levesque and Fast decided to tap in to their professional networks to find a construction project still in the planning stage that could serve as a demonstration site.
They found two.
One was a conventional five-story commercial building with first-floor retail and four floors of residential use planned for Somerville, Massachusetts. Designers opted for a hybrid mass timber construction technique, combining CLT floors and more conventional stick wood framing.
The other was Fairbanks Museum & Planetarium in St. Johnsbury, Vermont, where Executive Director Adam Kane had been trying to build an addition for nearly a decade. The museum board had originally agreed to use locally sourced nail laminated timber (NLT) – a different technique of binding dimensional lumber together – but when covid-19 struck, work came to a screeching halt. “It was a crazy, inflationary period for lumber,” Kane said. “The bids that came in for the work were 60 percent higher than the original construction estimate. We had no choice but to delay the project.”
And during that delay, Kane connected with NEFA.
“Suddenly, things sort of synced up,” Kane said. “We formalized a partnership, and as part of that arrangement, the museum was given the eastern hemlock CLT panels that had been manufactured for the proof-of-concept work.”
Because the original plans had called for nail laminated panels, the switch required only a modest amount of redesign from the project architect. The CLT panels and glulam beams arrived in March 2023. “It went together like an erector set,” Kane recalled.
The partnership with NEFA also helped the museum land a $350,000 grant from the federal Northern Borders program, with a proviso that “we would host tours and workshops – to be a demonstration site for engineers, architects, and construction companies,” Kane said.
The museum has amply fulfilled that requirement. Over the past year, hundreds of building professionals have walked through the Fairbanks addition’s two floors and rooftop space featuring the glulam beams and CLT panels. Visually stunning, the eastern hemlock’s warm, slightly red-tinted hues complement the darker interior of the original 1889 brick building – a combination of old and new that fits the museum’s scientific mission and image.
Kane couldn’t imagine a more fortuitous turn of events, and he’s become an advocate for regionally sourced CLT.
“You just need to have the local production,” he said. “If that piece gets sorted out, you’d have the demand here in the Northeast.”
While no one is offering a prediction on when a northeastern manufacturing plant will open, the two demonstration projects immediately led to the next best thing. Sterling Structural, North America’s largest CLT manufacturer, has initiated commercial production of eastern hemlock CLT sourced from New England. The company is producing the hemlock CLT at its Illinois facility and promoting it to the northeastern construction market.
Since covid, “interest in structural CLT has grown exponentially,” said Michaela Harms, senior director of mass timber at Sterling Structural. “There’s been a big change in the way we look at new buildings, and people want to work in beautiful spaces. Engineers like CLT for its strength and lightness, architects for its aesthetics, and owners with carbon action plans for its lowered embodied carbon portfolio value. Sustainability is really driving it.”
From her perspective, adding eastern hemlock to Sterling’s portfolio is a no-brainer. It doesn’t require retooling production lines or acquiring new machinery. CLT manufacturers can already handle multiple species, including both soft- and hardwoods, and typically build panels in standard configurations. When Fast and Levesque reached out to her, Harms said there was no hesitation.
“Eastern hemlock’s supply chain is a little less sophisticated right now, but we hope with this project to spur increased supply,” she said. “We’re always interested in ways to help grow the industry. We do see growing demand on the upper East Coast and we’re very proud to support local economies.”
Back to Bar Harbor
The very first commercial customer for Sterling Structural’s eastern hemlock CLT panels is Jesup Memorial Library in Bar Harbor.
Matt DeLaney’s experience managing the addition to the library has much in common with that of Adam Kane at Fairbanks Museum. The two have spoken several times over the past year about their experiences as eastern hemlock CLT pioneers. Beyond the obvious aesthetics and the construction advantages of the material, there’s a story of environmental and economic sustainability, of support for local businesses, and of connection to nearby forests, which seem to capture the imagination of those underwriting multimillion-dollar building projects.
Fundraising for the library addition “had been going on for a long time, and I think there needed to be an infusion of new energy,” DeLaney conceded. “And it turned out that mass timber was very exciting to a lot of our donors. They’re very interested in protecting the climate, in economic resiliency, and in environmentally friendly buildings.”
DeLaney believes that interest in CLT will spread quickly throughout the Northeast. Before the library addition was completed, he was already scheduling dozens of visits from curious contractors and engineers. He predicts exponential growth in mass timber buildings, sparked by the vision and hard work of people such as Peggi Clouston, Charles Levesque, Andrew Fast, and scores of others who provided advice and support.
“I swear to God, if I did not get covid and start picking up the phone and calling everyone, I don’t know if it would’ve all come together,” he said, back at the door of his miniature office. “It was the willingness of people to share credit, share connections. There’s a sharing culture around here that you wouldn’t see everywhere…. But here it was just people saying, ‘Gee, this is going to be good for the woods. Oh, this is going to be good for guys who are loggers; this should be good for guys in the sawmill.’ And you could just see the whole mass timber story develop.”