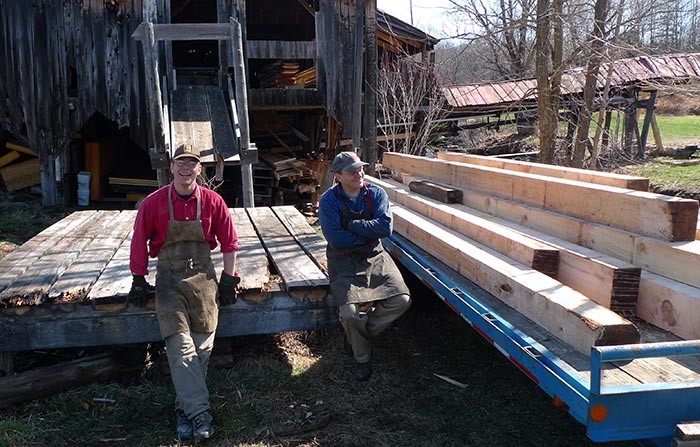
When Garland Mill began operations in 1856 – five years before the start of the Civil War – there were more than 600 water-powered sawmills in New Hampshire. One hundred-sixty years later, the Lancaster mill is one of only three water-powered sawmills still in operation in the state.
The water that powers the mill comes from Garland Brook, an inconspicuous little stream flowing from the Kilkenny Mountain Range, which rises to the east of the mill in a series of rugged summits, some higher than 4,000 feet. Just upstream from Garland Mill, the brook seems narrow enough to cross with a good leap, but at certain times of year there is enough water here to continue the work of sawing lumber.
The mill, and its sister timber-framing and construction company, have allowed cousins Ben and Dana Southworth to make a living in the business they purchased from their fathers in 2010. Garland Mill now produces between 30,000 and 40,000 board feet of lumber each year, with the majority of that used by Garland Mill Timberframes, the timber framing and construction side of the business. Most of the logs sawn here are white pine, sourced from within 20 miles of the mill and purchased from a handful of local loggers the Southworths have worked with for years.
“I can effectively saw for only two months each year, in early spring and late fall [when the brook is flowing],” said Dana Southworth, who oversees the milling side of the business. “We’re strategic in what we cut. We can saw a 35-foot timber without too much trouble. It’s pretty difficult to go out and buy something like that.”
The Southworths are the third set of second-generation mill operators at Garland Mill. Original owner Eben Garland sold the mill to his son Charles. Together, the Garlands ran the mill for 32 years, before selling it in 1888 to William Alden, who eventually sold it to his son Harold. The Aldens owned the Garland Mill for 86 years, and Harold Alden continued to run the mill until he was in his seventies.
In 1973, Yankee magazine ran a “House for Sale” feature on Garland Mill and the accompanying house and surrounding property. Some 300 buyers showed interest in purchasing the property, but most did not have any intent to maintain mill operations. One who did was Tom Southworth, a businessman from Philadelphia, who moved north with his wife, Nancy, and their young family. Tom apprenticed at the mill with Harold Alden for nearly a full year before buying the place in 1974. Three years later, his brother Harry migrated north with his family, and joined his brother in the mill business.
The younger Southworths grew up in Lancaster, helping out at the mill before moving on to other places and other work, Ben to various locales in the U.S. and to Norway for a time, Dana to a master’s degree in international economics and several years working in Washington, D.C., and the post-communist Balkans. But the pull of home and the sweet smell of sawdust proved strong: Ben returned to Lancaster and the mill in 2002, Dana in 2004, and they worked out a five-year buyout plan with their fathers, taking over the business in 2010.
“Working with both my hands and my mind is really satisfying,” said Dana. “And I wanted to come back to this place to be with my family and raise my children close to the people I love most.”
Garland Mill has maintained its small town sense of community, donating timberframe structures for the local skating rink and trails association and a warming hut for the town’s Mount Prospect ski area.
While Dana manages the mill and some of the timberframe design work, Ben handles whole-house construction and design of energy efficient houses. Together they manage the innumerable aspects of running a small business, from sales and pricing to planning and scheduling projects. Like their dozen employees, both Southworths can handle each part of the business if necessary – milling lumber, fitting frames, raising timbers, and fixing the myriad mechanical problems that arise when operating a 160-year-old mill.
“When my uncle bought the mill, Harold Alden told him he’d have to know how to fix everything,” said Dana. “That’s still true. There are no more nineteenth-century millwrights running around. You just have to roll up your sleeves and do it.”
The millwrights may be gone, but the power at Garland Mill is generated much the same way it was 160 years ago, albeit with some minor modern upgrades. Water flows from the brook through a penstock (plastic now, rather than wood) to fill the wheel pit. As the water falls into the wheel pit it hits the diagonal fins of the turbine, causing it to turn. The turbine spins a vertical shaft, creating mechanical power. An array of shafts, pulleys, and flatbelts allows the sawyers to direct that power to where it’s needed. If the brook is flowing and there’s no sawing to be done, that power is sent to the grid by way of a small electricity- generating turbine Tom and Harry Southworth installed in 1982.
“It’s very simple technology, but well thought out,” said Dana.
When the mill is running, the floor of the building vibrates intensely with the power moving through a series of belts and pulleys. Each log is pulled into the mill by a heavy chain operated by a lever. Dana and brothers Luke and Seth Colby, who are both electricians as well as sawyers, heft the log into place with peaveys, and a belt moves it toward the 28-horsepower, 50-inch-diameter circular head saw. The brook also powers an edger, planer, and trim saw, as well as constantly moving conveyor belts that transport slab wood into the bed of a 1965 GMC pickup outside and sawdust to a covered shed at the other side of the mill building, where local farmers collect it for use as livestock bedding. Finished timbers are moved along rollers to the end of the building, where they’re collected by forklift and stacked in one of the storage sheds outside.
Roughly 80 percent of the wood sawed at Garland Mill is used for Garland Mill Timberframes’ projects, which typically include a half-dozen structures each year, ranging from barns and simple cabins to carefully designed, energy efficient homes. What building lumber they don’t saw at their own mill, the Southworths source from local commercial mills, like Poulsen Lumber in nearby Littleton.
Logs that arrive at the mill are stacked and scaled next to the mill pond, then rolled into the water, which keeps potentially damaging bugs out of the logs and helps maintain the moisture level in the wood, making for easier sawing when the time comes.
On an unseasonably warm day last December, with the brook ice-free, Dana Southworth and the brothers Colby took advantage of the still-flowing water, hauling logs in from the mill pond and sawing large timbers. In the woodshop across the pond from the mill, Liz Friereman carefully and precisely fitted together pieces of a large cruck frame: two huge, curved cedar timbers notched expertly and exactly to hold other sections of the frame that will become a screened porch for a repeat client. A framing crew was working on site, as well.
Garland Mill is a display of classic Yankee industriousness, keeping things simple and creating something both useful and beautiful, something built to last longer than the people building it. It’s hard work, but for Dana and Ben Southworth, this is where they want to be: where they were raised, where their fathers made a life and a living before them.
“We have a fascination with and an emotional attachment to the business,” said Dana. “But we also really enjoy the work, and from a practical point of view, the business model works.”
Discussion *