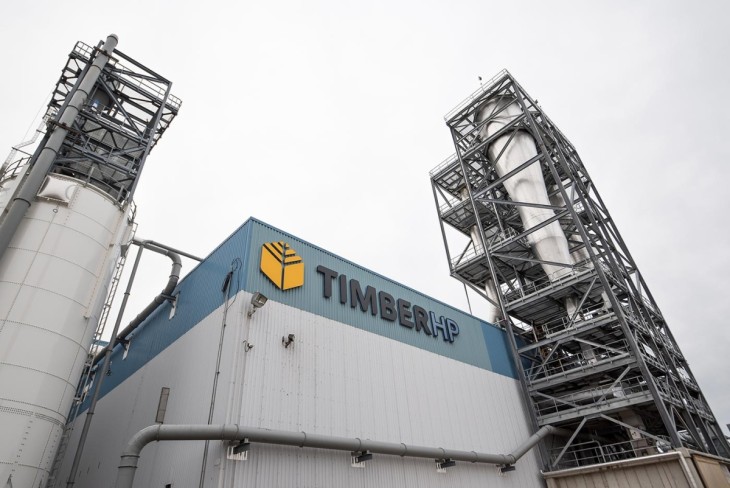
Luck is what happens when preparation meets opportunity. — Seneca (C. 4 BC–AD 65)
For many observers of Maine’s forest products industry, the 18-month period between 2014 and 2016 felt like the end – full-stop, definitive – of an era. Five paper mills fell like dominoes, one after another. The names of the towns rolled off the tongues of local news anchors: Old Town, Millinocket, Bucksport, Lincoln, Madison. Elected officials promised help in the form of retraining the workforce, but there was little they could do or say to ease the shock; in most cases, the mills had been the largest employers in town for several generations, and the taxes they paid funded such essentials as local schools and emergency services.
Once deemed Maine’s “imperial industry,” the state’s pulp and paper business had teetered for decades, beset by multiple woes, including declining demand for newsprint and coated papers, losses in raw materials thanks to insect infestations in northern forests, competition from new mills both foreign and elsewhere in the United States, and decisions made in boardrooms far from the mills – and the communities they supported. While the dominolike debacle didn’t entirely stop papermaking in Maine, the six paper mills that survived after 2016 represented a husk of an industry that shed 22 mills in the state over little more than a decade.
Accompanying the closure of those mills was the erasure of an estimated 13,000 jobs. In addition to the loss of those high-paying manufacturing jobs, impacts from the shutdowns reverberated up and down the industry’s supply chain, decimating the marketplace for low-grade logs, wood chips, and other sawmill byproducts. The loss of low-grade wood markets meant less profitable timber harvests and fewer opportunities for landowners to subsidize noneconomic forest stewardship activities.
The last bone to fall was an outlier, and maybe that made it the most challenging to accept. Madison Paper Mill, rising above a bend in the Kennebec River, occupied two adjacent footprints – one a late 19th-century brick-faced building secured to the banks by a granite foundation, where Great Northern Paper Company produced its first newsprint; the other a modern steel structure that arose in the early 1980s, financed by a joint partnership between the Finnish concern Myllykoski and The New York Times Company.
The $200 million upgrade promised to create a generations-long future based on cheap hydro-power and state-of-the-art machines producing supercalendered (high-gloss) paper. It represented the direction the state had urged on the industry – invest in new equipment and automation, switch output to higher value products, and take advantage of the natural and human resources already available. When UPM-Kymmene Corporation – the world’s largest magazine papermaker – acquired the mill as part of a $1.3 billion deal to buy Myllykoski in 2011, the town’s future in paper production seemed secure.
“No one here believed they would ever shut this mill down,” said former Town Manager Tim Curtis, who grew up in Madison in the 1970s and later returned with his own family in 2006. “They thought they’ll never shut this mill down because it was built in the 1980s and it was the most efficient mill of all those that made supercalendered paper. The work crew was very proud of their efficiency record.”
“That machine was just, you know, humming right along,” Curtis added. “If you’d been in there when they were making paper, you’d see a paper machine run at 60 miles an hour, moving raw material from one end, 2,000 feet down, and coming out as a roll of paper in like a minute, just constantly spooling these big, huge rolls.”
However, within five years of the acquisition, UPM mothballed the mill, padlocked the gates, and worked with liquidators to sell off assets. As Curtis tells it, the company sold the hydro capacity to a power generator, peddled off the machinery piece by piece, and sold the existing wood and parking lots to neighboring property owners.
“They weren’t hiding anything. They were saying, we’re going to split this up so it can never be used to make paper again,” Curtis said. “And now people were saying this place was going to be a ghost town.... Everything’s going to close down, and housing values are going to plummet, and everybody’s going to move out.”
Why Not Make it in Maine?
As Madison residents began to ponder the prospects of the town’s mill-less future, another discussion about the future of Maine’s forest products was taking place 60 miles away in Belfast, a town of about 7,000 set on the western shore of Penobscot Bay. Belfast residents Josh Henry, a University of Maine chemist, and architect Matt O’Malia discovered that they shared an interest in developing building materials that could substantially reduce the carbon footprint of housing.
“My whole interest in science and engineering was about the environment and technologies, especially renewable energy technologies and energy conservation technologies,” said Henry. “I’ve always been fascinated with energy and how we generate it, how we conserve it.”
O’Malia had recently founded a company, GO Logic, that emphasized “passive house” concepts, a science and engineering-based approach to home design and construction. By focusing on the building envelope – especially on insulation, windows, and doors – the passive house approach promises to reduce home energy consumption by 80 to 90 percent. If adopted industry-wide, it could have a significant impact on U.S. carbon emissions.
“I got excited about that because Matt was convinced that this was something we could do on a massive scale,” Henry said. “The idea being, if you focus on the building envelope and reduce energy consumption by that much, then you don’t need things like an oil boiler in your basement. You are phasing out some of the more expensive HVAC mechanical items like heating, ventilating, and air conditioning, doing a one-for-one cost swap with the building envelope. That was really exciting to me because I firmly believe that for us to take a step forward in terms of environmental technologies, the first things that we’re going to be able to achieve are things that are cost competitive.”
In 2016, the two formed GO Lab, Inc. to produce cost-effective, sustainable replacements for existing building supplies. One of the first challenges the company took on was insulation. Traditional house insulation, including the pink fiberglass batt found in many northeastern homes, can make buildings more energy efficient, but because the manufacture of insulation materials is either highly dependent on, or directly derived from, fossil fuels, it can take up to eight years of energy savings to offset the carbon emissions involved in installation.
As Maine natives, O’Malia and Henry wondered if the forest might provide an alternative.
“The only thing that we don’t do with wood in the homebuilding, housing, and commercial building sector is insulation,” Henry said. This lack of a domestic, wood-based option struck him as odd, especially after he discovered that wood-fiber–based insulation products had been available in Europe for the past 25 years. By his count, there were some 15 mills making wood-fiber insulation in three product formats – a loose fill, a batt, and a board – representing a billion euros in top-line revenue. Shipping it was cost prohibitive. But why wasn’t it produced on this side of the Atlantic?
Henry and O’Malia took the question to Germany, where they found fellow entrepreneurs with a shared environmental commitment who were eager to help them. Even now, Henry seems incredulous at the generosity they encountered.
“For whatever reason, they helped us, made a lot of good partnerships, and they gave us a lot of insight into the business pro forma of how they were doing it in Europe,” he said. “And we just took that and transposed it to North America.”
If wood-fiber insulation sold on the basis of consumers’ preferences for environmentally-friendly products in Europe, the GO Lab team quickly realized that the product could be even more competitive in the U.S. market. According to Henry, the price of feedstock (the raw materials) was a third to a fourth less expensive as in Europe, due to the abundance of sustainably managed forests here.
Not only that, but home construction contractors, who make the majority of buying decisions, had good reason to spec the product, too. Builders could avoid the itch and irritants of fiberglass particles that come into contact with skin during installation, and avoid the costs of protective gear. They also wouldn’t need to worry about air quality, disposal of nonrecyclable remnants, or plastic microbeads and dust from cutting board insulation.
Henry called it a “triple-win.”
“We’re able to deliver a product to customers here in North America that is green, that is renewable and recyclable, nontoxic, and carbon storing,” Henry explained, “but it is also cost competitive with all the other products on the market in the insulation space: foam, fiberglass, mineral wool, cellulose. It performs equally well, actually performs better. It’s kind of a no brainer.”
Pieces Fall Into Place
This is the moment in the story where we tend to get ahead of ourselves. Cut to the chase, a voice inside tells us. Get to the point. Call it the “Madison Miracle.”
In 2019, Henry and O’Malia’s new wood-fiber insulation company, TimberHP, acquired the Madison Paper mill for $1.4 million. The company was able to recoup more than half of that price by scrap-selling wire and pipe that the liquidators had left behind. It struck a deal with the hydro dam’s new owner to purchase renewable power at an advantageous inside-the-gate, pre-grid wholesale price. And in a development that might seem miraculous to an outsider looking in, TimberHP acquired the machinery it needed to manufacture its insulation product from a German mill when that mill’s owner, Dieffenbacher, decided to change its business model.
“They’re a big manufacturer of medium and high-density fiber board,” Henry explained. “And they said, ‘we’re going to close this facility to focus on our core products. And we don’t really want to sell this to our competitors.’”
So TimberHP bought $40 million euros worth of precision German machinery for $2.5 million euros.
Machinery? Check.
Manufacturing facility? Check.
Market opportunity? Proximity and access to feedstock? Check and check.
But miracle? Let’s not check that box quite yet.
A Skilled and Motivated Workforce
“None of this happens because of the force of will, intellect, whatever,” Henry said on the mill floor this past winter, walking along a 500-foot “batt line,” rising eight stories into the air. “It doesn’t happen from the talent of one person. We’ve benefited from the talent and the knowledge of everyone who operated this facility beforehand.”
That includes Joe Clark, who worked at the UPM mill maintaining the hydro stations and boiler house, took up shop-keeping after the mill closed, and now oversees mechanical and utilities support for TimberHP.
He got the call from another former UPM employee, electrician Martin Troy, who literally kept the lights on in the mill after it closed. “Marty said, ‘Hey there, the guys who bought the mill are looking around. They want to understand the boiler plant,’” Clark explained. “He said, ‘So you should meet them.’”
Clark agreed to meet Henry at a breakfast place across the river in Anson. He was on his guard. Several potential buyers had swung through town with big ideas but little groundwork and even fewer resources, financial or otherwise.
“Some developer comes in and they promise the moon. Then they sneak away under the cover of darkness. Next one comes in, and it’s the same thing over and over and over,” Clark said. “But you hang your hat because you don’t want to leave…. There was talk about growing marijuana plants, and all sorts of different things, and none of them made sense.”
Immediately, he sensed a difference with TimberHP’s approach.
“I like to tell people, Josh had me at hello. He’s just so sincere and genuine that he’s just one of the guys you want to help,” Clark said. “So anyway, I signed on as a consultant. At first it was part time, and then as things got more involved, I became full time.”
In short order, TimberHP had 80 years of Madison Paper mill experience in Troy (29 years), Clark (26 years), and Chief Operating Officer Rick Veinotte (25 years).
The company also drew on the experiences of local people such as operations manager Jessica Vigneault, a chemical engineering graduate of University of Maine who had worked for more than a decade in the paper industry. When TimberHP arrived in Madison, she was working on the Number Two Paper Machine at the Sappi mill in nearby Skowhegan. A neighbor stopped her on the road and asked if she’d heard about some of the opportunities available with TimberHP.
Now she’s overseeing the entire manufacturing process. Vigneault likes to say she’s traded the tanks and pumps of pulping and bleaching operations for the cyclones and blowers involved in making wood-fiber insulation.
“I oversee a team of people who are responsible for everything from moving chips in the woodpile to shipping final product out the door,” she explained after a long day troubleshooting the second continuous process line at the mill. “This means that I need to remove as many barriers as possible for work getting done by those crews. I troubleshoot equipment that isn’t working properly, or designed properly. I work with the operators to make the process easier, with fewer steps, and error proof. Make steps easy to get right and hard to get wrong.”
“We have the best operators in Maine,” she added. “We have people with extremely varied backgrounds who wanted to come here to be part of this project, and with that ambition came a drive to study and learn how to run this new equipment.”
Help with Start-up Costs
In addition to acquiring a mill in reasonably good shape, and having access to a highly experienced workforce, O’Malia and Henry were able to leverage a variety of state and federal funding programs that prepared the company to complete the journey from great idea to actual production.
Back in that 18-month stretch of paper mill closures, the Maine Forest Products Council (MFPC), the Maine Department of Economic Development (DECD), University of Maine, and quasi-public agencies including Maine & Company and The Maine Development Foundation had met frequently to try to figure out how to minimize the damage.
“We were losing our low-grade markets,” said Patrick J. Strauch, executive director of the MFPC. “We lost five pulp mills in a short time, decimating our outlet for softwood. We also lost some biomass plants, and biomass was an important part of the sector as well.”
Convened by U.S. senators Angus King and Susan Collins, with initial funding from the U.S. Economic Development Agency, the working group analyzed global markets, economic forecasts, the local supply chain, and labor markets to create a new future for one of Maine’s leading heritage industries. Members engaged in community listening sessions and sought out opportunities to build on existing infrastructure. They helped communities and entrepreneurs identify funding sources for new development plans.
According to Yellow Light Breen, CEO of the Maine Development Foundation, the resulting Forest Opportunity Roadmap wasn’t a plan for a post-paper Maine, but rather one that would champion greater industrial diversity, innovation, and technology to better utilize the state’s wood supply in the future.
“It might have begun from a crisis-response mentality,” Breen said, “but it quickly shifted to an opportunity-focused project. After all, we had 16 million acres of mostly privately held, sustainably certified forest that was a climate-friendly, fossil-fuel alternative. If we pointed at the right opportunities, we believed we could turn it around.”
Emphasizing Maine’s forest assets, existing workforce, and industry infrastructure, the roadmap aimed at a 40-percent increase in economic growth by 2025. It called for investments in the remaining paper mills in order to switch production to container board, packing, and labels. The roadmap also supported the conversion of particle board plants in the northern tier of the state, expansion of tissue production, and research and development into new products such as biochar and cross-laminated timber. And it advocated for free training programs – not only for displaced workers, but also for a new generation of high school and college graduates whose presence would attract new forest-based manufacturers.
“I can’t say our efforts put TimberHP on the map, but we’ll take credit for creating the environment,” Strauch said. “We all got pretty organized in understanding what Maine has to offer, what are its strengths and weaknesses, and what are the kind of companies were looking for that could provide that low-grade market that we were missing. Because that’s the key – to have good markets for all parts of the tree.”
Thanks in part to that groundwork, when TimberHP – and its annual appetite for 200,000 metric tons of wood chips – needed seed money, local, state, and federal agencies understood the context.
Curtis, the former Madison town manager (and now Somerset County’s administrator), described sitting in a room with officials from the DECD, the Finance Authority of Maine, and Coastal Enterprises, Inc. By combining everything from local tax breaks to grants and low-interest loans, the group managed to put together a $4 million package of incentives, guarantees, and support that helped TimberHP cover start-up costs.
“And it wasn’t just for TimberHP,” Curtis said. “It was a big deal for the sawmills in the state because that’s a lot of their byproduct – sawdust and chips and biomass – they could sell.”
Breen acknowledged that the $4 million incentive package represented only a small piece of the company’s financing, which included $130 million that TimberHP raised in the municipal bond market in 2023.
“But I think it shows that a moderate amount of money injected at the right time can be catalytic,” he said. “The Madison project was the result of a long process during which the community did everything it could to make the mill reuse possible.... And you had a bunch of industry leaders who really put in the effort and committed to a vision for the entire industry, from independent loggers, trucking and transport, and sawmills, right up to the manufacturers themselves.”
Rolling Out
Fast forward to 2024. A year after the company held a high-profile “log cutting” ceremony to open the plant with 60 employees, the former university chemist, Henry, is still adjusting to his new world. The company is feeling some heat from customers because it can’t deliver its new Timber-Batt product quickly enough to satisfy demand.
But that’s a good problem to have, isn’t it?
“It’s one thing to be CEO of an idea, to be CEO of a company of promise,” Henry said. “It’s very different to be CEO of a company that delivers a product. And the only way I can be successful is with people like Jessica [Vigneault]. I’m fortunate because, like her, everyone here displays such extreme dedication, creativity, and good old-fashioned Maine grit.”
When all three continuous process lines are running this summer, TimberHP expects to count 140 people on the payroll, with operations increasing from four 24-hour days to seven. There’s even talk, which Henry won’t confirm, of a second facility on the West Coast.
Walking past bundled packages of batt ready for delivery, Henry reflected on the fact that even though continuous process lines are producing up to 7 metric tons an hour, business outcomes are measured by longer time frames. He rejected the “Madison miracle” story line. Success has been neither easy nor quick, he said, and he cautioned that it still is not guaranteed.
“I kept on telling my wife, ‘We’ll probably know in six months or whatever,’ and that was starting in 2015,” Henry said. “So there was a lot of thinking that we’re making progress, forward steps, not realizing how far we really were.... Because I didn’t know enough about the process. And just looking at what this facility looked like when it was a paper mill, it was so complex, and realizing we’re effectively rebuilding that complexity from the ground up.”
Strauch, like Henry, is wary of magic-bullet narratives and straight-line success stories. A community’s ability to rebound has little to do with chance and a lot to do with long-term planning, he said.
“Most communities really didn’t know what to do when their mill closed, or what they had, and they would have benefitted from kind of an organized strategy to think about their futures,” he said. “Madison knew what they had – they had defined assets, and they worked hard to market their facility. They had a pretty well-trained workforce, a lot of talent, a lot of millwrights, a lot of boiler operators who knew that facility. They weren’t lucky when Josh and company came looking for a facility – they were ready.”