Henry David Thoreau admired a hand-made axe handle in a journal entry made more than 150 years ago: “Those made by hand are considered stronger than those which are turned (on a machine), because the outline conforms to the grain . . . I like to see the farmer whittling his own axe helve as I did E. Hosmer, a white oak on the 27th.”
Times have changed, but Thoreau’s sentiment is as true today as it was back then. When it comes time to replace the handle on your axe, why not forgo the trip to the hardware store and whittle one yourself? You needn’t be a distant relative of E. Hosmer to accomplish such a feat. All you need is an axe, a drawknife, a spoke shave, a rasp, and a sharp knife with a flat bevel. Here are some instructions to get you started.
Step One
Choose a freshly cut bolt of ash, hickory, sugar maple, yellow birch, or hophornbeam. A firewood cutter would be a good source. The wood should be green and straight-grained, without knots, about 10 to 16 inches in diameter. It is surprising how easily green wood can be shaped with sharp hand tools; it’s like cutting frozen cream cheese.

Step Two
Split the bolt into quarters, sixths, or eighths; each split piece, called a billet, should have at least four or five inches of bark. The one guiding principle to keep in mind when making an axe handle is to keep the same annual growth ring in the center of the entire handle, from where it will enter the axe head to the fawn’s foot. That annual ring will be split by the wedge in the final step, and it will run in the same plane as the swing of the axe, providing the handle with strength and shock-absorption. All the splitting, hewing, shaving, and carving are done to provide an appropriately sized handle while holding to this principle.

Step Three
Score and hew, or split out, the triangle on the inside of the billet and remove the bark. Hew the surface smooth and trace on it an outline of the desired handle. The billet should be about one and one-half inches thick, oversized at the bottom for the fawn’s foot, and about four inches wide. The length of the handle varies with use. Handles used for shaping work are 19 to 22 inches, camp axes carried on trips are 20 to 26 inches, and those for chopping and splitting are 28 to 31 inches. A chopping axe handle length is often equal to the inseam of your pants.
Step Four
Following the pattern, score and hew the handle into rough shape. The outline and the center lines on the annual ring may have to be redrawn as the draw knife and spoke shave remove more wood. A shaving horse is useful, but a bench vice will work well, too. The area of the handle that fits into the eye of the axe head is kept as an oversized rectangle of wood; the shaft is shaped into an oblong profile that has the ratio of one to two, thickness to width. This keeps the handle from turning in your hands during use. Many of the handles we have are ¾ inch thick and 1½ inches wide. The fawn’s foot can be shaped with a spoke shave or rasp, but a sharp knife works best when the wood is green.
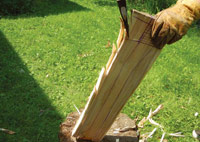
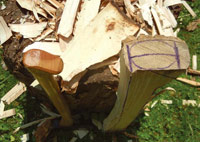
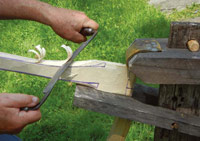

Step Five
The handle is nearly finished now, but it should be dried for a few weeks. Seal both ends to keep them from drying faster than the rest of the wood and checking. A cheap way to do this is to mix equal amounts of white glue and hot water, then smear the paste on the end grain. Then, hang it up and let it dry. When dry, the handle can be further finished by sanding, scraping with a piece of broken glass, or smoothing with a spokeshave. Finally, treat it with a couple of coats of boiled linseed oil, thinned with turpentine.
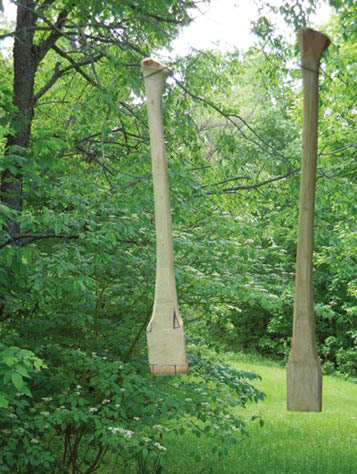
Last Step
The last step is to hang the axe head on the dried handle. A straight-grain wooden wedge is used to keep the joint tight and safe. The slot for the wedge is either sawed or split along the center annual ring, to half the depth of the eye. Sawing provides more control, but splitting can work well if the wood is clamped tightly to limit the depth of the split. Great care in shaping the wood for a tight fit is essential. Take a little at a time with your spokeshave or rasp, and keep checking the fit until you have it right. Tapping the squared-off part of the fawn’s foot should pull the axe head onto the handle.
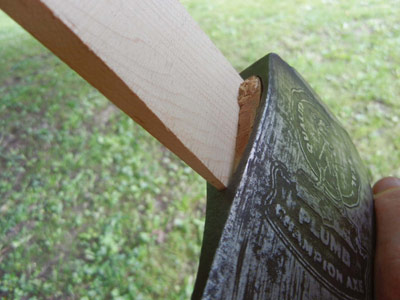
The wedge can be sawed out on a band saw, and should be an inch or more longer than needed; it should be as wide as the slot, and thicker. Insert the wedge and drive it in until tight, then wait a few days and pound it in more. With the wooden wedge in place, apply a wood-swelling fluid such as Chair-Loc or Wonderlok’Em Tite Chairs, available at most hardware stores. This product will swell the wood, then solidify inside it, assuring a tight fit. Here at home, we have handmade axe handles that we’ve used every year for over thirty years; they are as good as the day they were fitted to the head.
Discussion *